Shotcrete / Concrete Plants
Portfolio of Projects - Shotcrete/Concrete Plants
Newmont Mining Corporation
Getchell Gold Corporation
Great Basin Gold Ltd.
Hecla Mining Company
Thiessen Team
Newmont Mining Corporation
Midas Mine
Carlin, Nevada, USA
Size / Capacity: 40 ton/hr
This plant comprises of a series of screw conveyors, bucket elevator, shotcrete bin, wet-mix screw conveyor and PLC control discharge system.
Services Provided
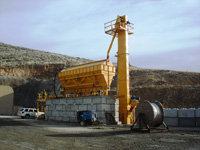
- Conceptual Design
- Struct./Mech. Engineering
- Design & Supply Of Control System
- Supply/Fabrication of all Equipment
- Supervision of Equipment Installation
- Commissioning and Training
Supplied Equipment
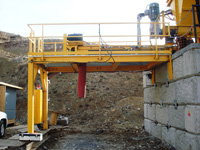
- Shotcrete Weigh Hopper
- Three Screw Conveyors
- Mixing Screw Conveyor
- MCC/PLC System
- Pneumatic Control System
This plant is designed to receive pre-blended shotcrete from bulk carriers, and batch wet mix automatically. The main shotcrete bin utilizes load cells to batch subtractively. The system will batch and mix the requested quantity of wet shotcrete in 1/2 cubic yard increments to a maximum of six yards. Water (slump) may be adjusted by the operator, entered as gallons per cubic yard. An automatic self-cleaning cycle is initiated following each batch. The controls have been simplified to allow each driver to operate the plant and minimal operator interface is required.
Bulk truck unloading is also automated and no dust collector is required. The shotcrete storage bin may be vented back to the truck while loading.
All areas of operation are monitored and fully interlocked. The system PLC is located in the batching console at ground level. As the system runs automatically, illuminated pushbuttons serve as function indicators and manual overrides. Alarms will sound in both the truck unloading area and batching area.
Getchell Gold Corporation
Turquoise Ridge Mine, Golconda, Nevada, USA
Size / Capacity: 65 tons per hour
Services Provided
- Conceptual Design
- Struct./Mech. Engineering
- Design & Supply Of Control System
- Supply/Fabrication of all Equipment
- Supervision of Equipment Installation
- Commissioning and Training
Supplied Equipment
- One Surface Plant:
- Shotcrete Storage Bin
- Bucket Elevator
- Three Screw Conveyors
- MCC/PLC System
- Pneumatic Control System
- Two Underground Plants:
- Two Shotcrete Weigh Hoppers
- Four Screw Conveyors
- Two Mixing Screw Conveyors
- Two Dust Collection Systems
- Two Shotcrete Diverters
- Pneumatic Control Systems
The Material Handling Team was commissioned to design and manufacture an automated bulk shotcrete processing plant for the purpose of bulk handling dry pre-blended shotcrete materials.
This plant was designed to receive shotcrete on the surface from custom 20-ton trailers and store in a 60 cubic yard surface bin. The shotcrete is then automatically distributed automatically via anti-segregation and anti-degradation systems to the 1250' or 1550' levels. The material is then weighed and fed through pre-dampener screw conveyors into waiting "Normet" transport vehicles. Following batching, automatic refilling from the surface initiates.
All areas of operation are monitored and fully interlocked. The system PLC is located on the surface and controls all underground operations via remote I/O.
Great Basin Gold Ltd.
Hollister Mine
Winnemucca, Nevada, USA
Size / Capacity: 20 ton/hr
This plant comprises of a skid mounted, 10 cubic yard bin, that has been modified to receive bulk bag material.
PURPOSE
- Batch shotcrete, concrete and cementitious grout.
SERVICES PROVIDED
- Conceptual
- Retaining Block Supply
- Design & Supply of Control System
- Supply of all Equipment
- Commissioning and Training
SUPPLIED EQUIPMENT
- 10 yard capacity Volumetric Plant (skid mounted and modified)
This plant is designed to receive pre-blended shotcrete from bulk Super Sacks, and batch wet mix manually. The bin utilizes a volumetric system to batch. The system will batch and mix the requested quantity as called. Water (slump) may be adjusted by the operator, either by dry product delivery gate height adjustment or alteration in delivered GPM.
Operators have full visual field of view between dry product transition and slumped product placed into a remix truck.
Hecla Mining Company
Green's Creek Mine
Admiralty Island, Alaska, USA
Size / Capacity: Two Yard/batch
This plant comprises of a weigh batch mixing system and PLC control Batch system.
SERVICES PROVIDED
- Conceptual Design
- Struct./Mech. Engineering
- Design & Supply Of Control System
- Supply of all Equipment
- Commissioning and Training
SUPPLIED EQUIPMENT
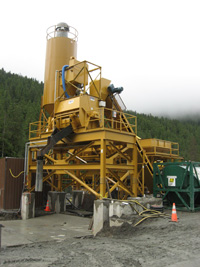
- Aggregate hoppers
- Weigh conveyor
- Pocket conveyor
- Single shaft Paddle mixer
- Water weigh hopper
- Cement silo and weigh hopper
- MCC/PLC System
This plant is designed to weigh all raw products and discharge into the mixer. After the desired mix time the discharge door is opened by the operator into a chute that feeds underground remix trucks.
All areas of operation are monitored and fully interlocked. The system PLC is located in the batching console at ground level. As the system runs automatically, illuminated pushbuttons serve as function indicators and manual overrides.
Thiessen Team
Big Timber, MT
Size / Capacity: 25 yard/hr Bulk or bagging Plant
This plant comprises of a aggregate drying/storage system, weigh batch mixing system and PLC control Batch system.
SERVICES PROVIDED
- Conceptual Design
- Struct./Mech. Engineering
- Design & Supply of Control System
- Supply/fabrication of all Equipment
- Construction and installation of plant
SUPPLIED EQUIPMENT
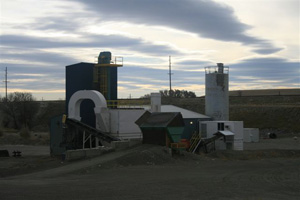
- Feed hopper
- Conveyors
- Aggregate bins
- Bucket elevator
- Scalping screen
- Dryer
- Screw conveyors
- MCC/PLC System
This plant is designed to. Weigh all raw products and discharge into the mixer. After the desired mix time the discharge door is opened by the operator into a chute that feeds underground remix trucks.
All areas of operation are monitored and fully interlocked. The system PLC is located in the batching console at ground level. As the system runs automatically, illuminated pushbuttons serve as function indicators and manual overrides.
PURPOSE
- Batch various mix designs to meet customers' demands