Grout Plants
Portfolio of Projects - Grout Plants
- Inco Limited - Birchtree Mine Deepening
- Hudson Bay Mining & Smelting - 777 Mine Project
- Newmont Mining Corp. - Deep Post Mine
- Advanced Construction Techniques - Diavik Mine
- Empresa Minera Iscaycruz S.A. - Iscaycruz Zinc Mine
- Schnabel Foundation Company
- Cominco Limited - Sullivan Mine
Slurry Plant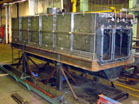
Inco Limited
Birchtree Mine Deepening
Thompson, Manitoba, Canada
The Material Handling Team supplied two separate fully automated, modular backfill systems for the Birchtree mine.
Both plants include a cement storage hopper with integral dust collector, screw conveyors to supply binder to a colloidal mixer, progressive cavity pump and fully automated control system. The first system is built around a 2500 Litre, four mill colloidal mixer, while the second design includes a 1000 Litre, two mill mixer.
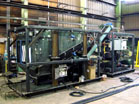
In addition to the equipment listed above, a 20 ton capacity storage hopper with pneumatic screw pump and air compressor was supplied with the second plant.
The plants are designed to be broken down into small modular pieces to allow them to be transported underground via the mine cage, and then re-assembled underground without any additional welding. Both systems were pre-fit, assembled and tested at our facility prior to delivery to the mine.
Each of the systems is designed to be frequently relocated through the mine, and was fabricated in four sections with quick-disconnects for electrical, air, and water services.
SIZE / CAPACITY
- 7.9 cubic meters per hour
SERVICES PROVIDED
- Conceptual Design
- Struct./Mech Engineering
- Design & Supply of Control System
- Supply/Fabrication of all Equipment
- Supervision of Equipment Installation
- Commissioning and Training
SUPPLIED EQUIPMENT
- 2500 Litre Colloidal Mixer
- 1000 Litre Agitation Tank
- Two Progressive Cavity Pumps
- 20 Ton Storage Silo
- Two Surge Hoppers
- Three Dust Collectors
- Six Screw Conveyors
- Rotary Screw Pump
- Air Compressor
- Structural Support Skids
- Protective Cages for Mobile Equipment
- PLC/MCC System
- Pneumatic Control System
- All Required Piping and Valving
Slurry Plants
Hudson Bay Mining & Smelting
777 Mine Project
Flin Flon, Manitoba, Canada
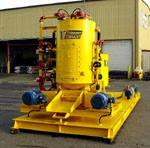
The Material Handling Team supplied a slurry plant for the HBM&S 777 mine expansion project. The supplied Thiessen Tornado system produces cementitious slurry required by a paste backfill plant that is used for ground stabilization in the underground mine.
The slurry plant features a 1350 Litre Colloidal mixer, agitation tank, progressive cavity pump, magnetic flow meter, and is supplied fully automated with an integrated MCC & PLC cabinet.
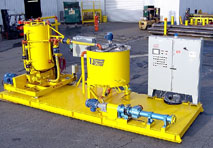
The Colloidal mixer produces slurry on demand: As the agitation tank drops to a predetermined low-level set point, additional colloidal mixer batches are initiated as required. Progressive cavity pump output and slurry flow readings are controlled by the main paste backfill system where the slurry is introduced into the primary backfill mixer.
Typical of all Thiessen Tornadoes, this system self cleans after every batch. The plant also features the upgraded Keller Mark III colloidal mills including an improved sealing system and automatic grease purging.
SIZE / CAPACITY
- 7.6 cubic meters per hour
SERVICES PROVIDED
- Conceptual Design
- Mechanical Engineering
- Design & Supply of Control System
- Supply/Fabrication of all Equipment
- Supervision of Equipment Installation
- Commissioning and Training
SUPPLIED EQUIPMENT
- 1350 Litre Colloidal Mixer
- 2000 Litre Agitation Tank
- Progressive Cavity Pump
- PLC/MCC System
- Pneumatic Control System
- Equipment Support Skid
- All Required Piping and Valving
Slurry Plant
Newmont Mining Corporation
Deep Post Mine
Carlin, Nevada, USA
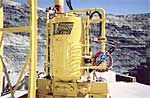
As part of a larger underground backfill system, the Material Handling Team designed a compact Thiessen Tornado 1350 slurry system supplied by a cement silo provided by Newmont Mining Corporation.
This plant supplies cementitious slurry to haul trucks loaded with aggregate on surface for initial backfill production, while construction of the main backfill plant underground is undertaken.

The slurry system was designed to work in three distinct modes. Initially, slurry was supplied on surface. The plant was then re-located and integrated into the main backfill system underground, to pre-slurry cement for the 6 cubic yard compulsory mixer. Thirdly, the backfill system has been designed to allow the slurry plant to again function as an independent slurry plant, when required.
SIZE / CAPACITY
- 7.5 cubic meters per hour
SERVICES PROVIDED
- Conceptual Design
- Struct./Mech. Engineering
- Design & Supply of Control System
- Supply/Fabrication of All Equipment
- Supervision of Equipment Installation
- Commissioning and Training
SUPPLIED EQUIPMENT
- 1350 Litre Colloidal Mixer
- Screw Conveyor
- Slurry Dispensing Head
- Silo Cone Modifications
- PLC/MCC System
- Pneumatic Control System
- All Required Piping and Valving
Mobile Grout Plant
Advanced Construction Techniques
Diavik Mine
Lac de Gras, NWT, Canada
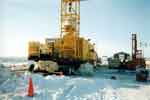
This plant is a self-contained, mobile grout production plant, consisting of two roadworthy containers joined as a single unit on-site. The on-board control room oversees automated grout production and monitors and records pumping data. Once on-site, the plant may tow as a single unit.
Cement is delivered via bulk bags to the plant at the bulk-bag unloader, external to the main structure. Admixtures, etc. are loaded on board by forklift and water is supplied from external sources, heated, when required.
Two Moyno progressive cavity pumps supply grout in various mixtures at varying pressures and flow rates to the boreholes. A third identical backup pump is used for water testing boreholes prior to grouting. Grout batching is fully automated and re-batches upon demand leaving the operator(s) free to concentrate on pump pressures, flows, and data processing. At the control console, a color touchscreen displays dynamic graphics of the batch process.
This entire custom plant was designed, fabricated, assembled, programmed, and tested in approximately 2 ½ months.
SIZE / CAPACITY
- 6 cubic meters per hour
SERVICES PROVIDED
- Conceptual Design
- Mechanical Engineering Design & Supply of Control System
- Supply/Fabrication of All Equipment
- Commissioning and Training
SUPPLIED EQUIPMENT
- Two Modified 40' Containers mounted on Modified Trailer Chassis
- Two Colloidal Mixers
- Four Agitation Tanks
- Three Moyno Pumps
- Bulk Bag Unloader
- Admix System
- Control Room with MCC/PLC System
- Pneumatic Control System
- Dust Collector HVAC System
- Onboard Generator and Compressor
- Fuel and Water Storage
- All Required Piping and Valving
Slurry Plant
Empresa Minera Iscaycruz S.A.
Iscaycruz Zinc Mine
Lima, Peru
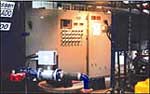
This automated 'Thiessen Tornado' system is used to produce cementitious slurry for a continuous paste fill plant for ground stabilization in the underground zinc mine.
This plant features an SD1000 automated Colloidal mixer, agitator tank, progressive cavity pump, mag-flow meter, PLC control system and MCC for continuous slurry output to the larger paste fill system.
Slurry is produced automatically on demand. As the agitation tank drops to a pre-determined setpoint, additional batches are initiated as required. Progressive cavity pump control and slurry flow readings are assigned to the main paste fill system where the slurry is introduced into a twin-shaft Pugmill along with other components.
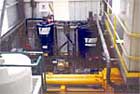
Typical of all 'Thiessen Tornado' plants, this system is self-cleaning, after every batch. The plant features the new Keller Mark III Colloidal mills with an improved sealing system and automatic grease purging.
This site is located at approximately 16,000 feet in the Andes and offers spectacular views in all directions along with the interesting culture of the people of the Peruvian Andes.
SIZE / CAPACITY
- 9.6 cubic meters per hour
SERVICES PROVIDED
- Conceptual Design
- Struct./Mech. Engineering
- Design & Supply Of Control System
- Supply/Fabrication Of All Equipment
- Supervision Of Equipment Installation
- Commissioning and Training
SUPPLIED EQUIPMENT
- 1000 Litre Colloidal Mixer
- 2000 Litre Agitation Tank
- Positive Displacement Pump
- Dust Collection System
- MCC/PLC System
- Pneumatic Control System
- All Required Piping and Valving
Grout Plant
Schnabel Foundation Company
Sterling, Virginia & Washington, D.C.

This unique batch plant is used to produce cementitious slurry for use in ground stabilization. The main components of the plant comprise of a cement silo and screw conveyor, Bentonite feed system, four mill colloidal mixer, agitation tank, dust collecting system, PLC control system, motor controls, and progressive cavity pump.
Slurry is automatically produced in the colloidal mixer upon demand and stored in the agitation tank. Here it is discharged at a controlled rate as required by the crane operator. The crane may be several hundred feet from the plant. The crane lowers large augers into the ground to be stabilized, mixing the soil with incoming slurry piped from the plant. Radio controls provide the crane operator with both a digital readout of the slurry flow rate and flow adjustment control. As the slurry agitation tank is drawn down, additional batches are called automatically.
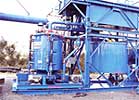
Cement is delivered into the silo pneumatically and Bentonite is delivered either in hand bags or bulk bags. Following each batch, water is reweighed and the mixer and slurry discharge lines are purged clean. This water remains in the mixer (scale), ready for use in the following batch, minimizing water wastage.
The grout plant and crane are both relocated throughout the country, to ground stabilization job sites for relatively short periods of time. The Material Handling Team is again proud to have worked with an industry leader in another leading edge technology.
SIZE / CAPACITY
- 36 cubic meters per hour
SERVICES PROVIDED
- Conceptual Design
- Struct./Mech. Engineering
- Design & Supply Of Control System
- Supply/Fabrication of all Equipment
- Supervision of Equipment Installation
- Commissioning and Training
SUPPLIED EQUIPMENT
- 3000 Liter Colloidal Mixer
- Cement Silo
- Two Screw Conveyors
- 6000 Litre Agitation Tank
- Slurry agitator
- Slurry Pump
- Water surge tank
- Dust Collection System
- Bentonite Storage & Feed System
- MCC/PLC System
- Pneumatic Control System
- All Required Piping and Valving
- Radio Controls
Slurry Plant
Cominco Limited
Sullivan Mine
Kimberly, BC, Canada
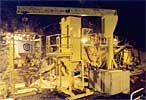
Located in the beautiful East Kooteney region of Eastern British Columbia, this underground lead zinc mine utilizes a compact Thiessen Tornado 1000 CRF plant.
This plant is located underground and was designed to break down for frequent transport by the mine personnel. The plant therefore features quick disconnects for all electrical and pneumatic connections.
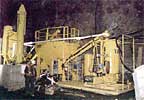
As with all Tornado systems, this plant features a Colcrete-Eurodrill colloidal mixer, runs unattended and is totally self-cleaning. This unit is controlled by a Modicon PLC and touchscreen.
Because of the distance from the surface, bulk cement bags are used for supply and the plant has a bag receiving hopper and screw conveyor.
SIZE / CAPACITY
- 16 cubic meters per hour
SERVICES PROVIDED
- Conceptual Design
- Struct./Mech. Engineering
- Design & Supply Of Control System
- Supply/Fabrication of all Equipment
- Supervision of Equipment Installation
- Commissioning and Training
SUPPLIED EQUIPMENT
- 1000 Litre Colloidal Mixer
- Cement Storage Hopper
- Three Screw Conveyors
- Dust Collection System
- Slurry Dispensing Head
- Bulkbag Unloader
- MCC/PLC System
- Pneumatic Control System
- All Required Piping and Valving