Backfill Plants
Portfolio of Projects - Backfill Plants
- Newmont Mining Corporation - Deep Post Mine
- Minera Meridian LTDA - Chile
- Getchell Gold Corporation - Turquoise Ridge Mine
- Kahama Mining Corporation - Bulyanhulu Gold Mine
- Cominco Limited - Polaris Mine
- Homestake Canada Inc. - Eskay Creek Mine
- Sistema Hidraulico - Portal de Entrada
- Sistema Hidraulico - Portal Salida
Cemented Rockfill Plant
Newmont Mining Corporation
Deep Post Mine
Carlin, Nevada, USA
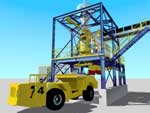
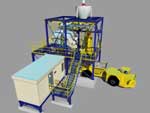
This multi-level plant is designed for automated backfill production at Newmont's Deep Post Mine. The backfill plant utilizes a twin shaft mixer at the 4084 level, to mix backfill, discharging directly into haul trucks.
Aggregate is delivered underground by truck to a 1300 ton aggregate storage silo before feeding the mixer. Cement and flyash are pneumatically conveyed from surface and stored in bins on the 4290 level. Here, a blend is produced for delivery to the backfill area or an underground shotcrete plant. Once in the backfill area, blended cement is conveyed directly to the mixer or alternately, to the colloidal mixer for slurry batching.
All process are controlled by the operator using PC control, as the operator interface. Fibre optics are used to communicate with the five PLCs in the system.
Redundant features in the backfill plant ensure reliability. In the event the slurry mixer is unavailable, water and cement may be metered directly to the mixer. Should the main backfill mixer be unavailable, trucks may receive aggregate and slurry at the upper truck bay, ensuring backfill production continues.
SIZE / CAPACITY
SERVICES PROVIDED
|
SUPPLIED EQUIPMENT
|
Cemented Rockfill Plant
Minera Meridian LTDA
El Penon, Chile
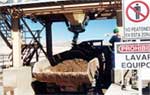
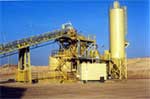
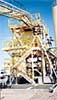
The Material Handling Team designed, manufactured, and commissioned this automated backfill plant. It is located in the driest location on earth, the Atacama dessert in northern Chile.
This plant combines cementitious slurry with coluvium (aggregate), known as 'chusca'. A Thiessen Tornado slurry system is utilized to prepare slurry in multiple batches and store it in a holding tank. Aggregate is stockpiled above a tunnel conveyor and is then conveyed to a pugmill via a conveyor scale.
The process is a hybrid system, using automated slurry batching combined with a continuous process at the pugmill where the aggregate and slurry are mixed before discharging to the backfill holding hopper and haul-truck. The system is mostly self-cleaning, using the Tornado's colloidal mixer and slurry pump to purge all lines, the pugmill and gob hopper.
This project was particularly challenging due to the complexity of coordinating the continuous processes to sized truckloads up to 20 tonnes. Two variable frequency drives (VFDs), a conveyor scale, and a variable speed/reversing peristaltic pump were utilized within the system to ensure consistent, high quality backfill.
The unique feature of this plant is the self cleaning purge cycle inherent within every batch. The system self-cleans in this manner and may continue this way for shifts of any duration. At the end of a shift, a wash formula, (water only), be run for a final cleaning.
SIZE / CAPACITY
SERVICES PROVIDED
|
SUPPLIED EQUIPMENT
|
Cemented Rockfill Plant
Getchell Gold Corporation
Turquoise Ridge Mine
Golconda, Nevada, USA
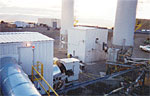

The Material Handling Team was the successful bidder in the design, manufacture and commissioning of Getchell Gold's Turquoise Ridge backfill system. The plant is comprised of silos, feeders, weigh-bins, diverters and mixers at various locations throughout the mine.
Cement and flyash from surface silos and aggregate from the surface batch plant are fed through borehole feed lines to a series of transfer and weighing stations underground. The material is then mixed in a 10 cubic yard Besser mixer where it is fed into haul trucks to be used in their underhand cut and fill operations.
The plant also includes a Thiessen Tornado 1000 on the surface which feeds cement slurry to the various underground levels where it is sprayed over development waste for the production of further cemented rockfill.
SIZE / CAPACITY
SERVICES PROVIDED
|
SUPPLIED EQUIPMENT
|
Concrete Batch Plant
Kahama Mining Corporation
Bulyanhulu Gold Mine
Tanzania, Africa

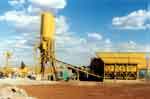

The Material Handling Team was commissioned by Kilborn SNC Lavalin to supply a complete concrete batching plant to be used for surface and underground construction at Sutton Resources' remotely located Bulyanhulu minesite in Tanzania, Africa.
In order to meet shipping deadlines, The Material Handling Team completed all design and fabrication, including all control PLC and MCC systems, in six weeks. A subsequent flyash upgrade was also supplied, which features their innovative bulk bag unloading system, and commissioning of the entire plant.
SIZE / CAPACITY
SERVICES PROVIDED
|
SUPPLIED EQUIPMENT
|
Cemented Rockfill Plant
Cominco Limited
Polaris Mine
Little Cornwallis Island, Nunavit, Canada
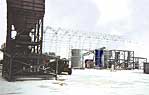
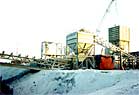

Located only 100 km from the magnetic north pole, the Cominco Polaris lead-zinc mine is the most northerly operating mine in the world. When working north of the seventy-fifth parallel, the Arctic Ocean only allows a six week window in mid summer to allow sea access by freighter. Polar bears, caribou, arctic fox and musk ox are seen almost daily, within the boundaries of the mine.
In this project undertaken by The Material Handling Team, 27 truckloads of equipment had to be dockside in Montreal within a few months or the project would be delayed for a year. The Material Handling Team delivered all equipment as required.
The plan called for 8" minus aggregate, permanently frozen by Arctic conditions, to be brought in by haul truck, conveyed and stored in a 375 ton bin. The rock was then fed by a series of apron feeders, vibratory feeders, and conveyors through a pre-heat stage and hot water rotary bath to a second 75 ton storage bin.
Here, a Thiessen Tornado, employing four Colcrete-Eurodrill colloidal mills combined a cementitious slurry with the heated rock. 30 ton haul trucks were then loaded with cemented rockfill for use in the underground mine. The heated CRF had to withstand unbelievable ambient temperatures approaching -70 degrees C, with wind chill.
A single Modicon PLC system with dual touchscreens was used to monitor and control the entire plant. The Material Handling Team also provided site supervision and startup assistance to Cominco in prime Arctic conditions, October to April.
SIZE / CAPACITY
SERVICES PROVIDED
|
SUPPLIED EQUIPMENT
|
Cemented Rockfill Plant
Homestake Canada Inc.
Eskay Creek Mine
Eskay Creek, BC, Canada
Eskay Creek Mine is located in British Columbia, north of Stewart and is one of Canada's premier gold mine operations.
The Material Handling Team was commissioned by Homestake Canada Inc. to design and manufacture a cemented rockfill plant. This batch plant, located at the mine's lower portal, mixes aggregate, cement, and water, yielding a premixed cemented rockfill. The plant incorporates a 3000 litre Teka pan mixer. The entire process runs automatically using a Modicon programmable controller and touchscreen, which is connected via a communications network to other PLCs at the mine.
This plant was prefabricated and shipped in modules. The Material Handling Team's contract included civil engineering, motor control center, erection supervision and operator training. This plant is equally capable of producing high quality concrete and shotcrete, in addition to cemented rockfill.
SIZE / CAPACITY
SERVICES PROVIDED
|
SUPPLIED EQUIPMENT
|
Concrete Batch Plant
Sistema Hidraulico
Portal de Entrada
Yacambu, Estada Lara, Venezuela
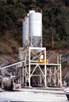
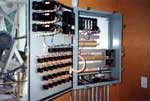
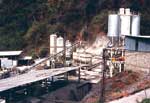
The Material Handling Team was contracted to design, supply, and commission a pre-mix concrete batch plant at the portal of this irrigation tunnel. This batch plant produces shotcrete and concrete for tunnel lining. This plant featured a 4 yd³ Voeller pan mixer and is PLC controlled. The plant was commissioned by Material Handling Team personnel who also performed operator training on-site.
This project involves a 24 km tunnel in Los Andes spurs, in western Venezuela. The tunnel is to supply irrigation water from the Yacambu valley to the neighboring Quibor valley. The contrast between the lush jungle environment at Portal de Entrada and the dry desert climate at the other end, Portal Salida is remarkable.
SIZE / CAPACITY
SERVICES PROVIDED
|
SUPPLIED EQUIPMENT
|
Concrete Batch Plant
Sistema Hidraulico
Portal Salida
Quibor, Estada Lara, Venezuela
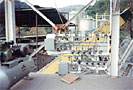
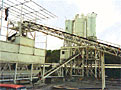
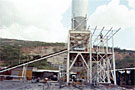
This project, as described previously in the Yacambu project, involves the same 24 km irrigation tunnel, in Los Andes spurs. As with the plant at Portal de Entrada, in the Yacambu valley, The Material Handling Team was contracted to design, supply, and commission a concrete batch plant at the Portal Salida featuring a Voeller pan mixer. This plant is also PLC controlled and included an Motor Control Center as part of the automated package.
The project itself involves tunneling from the outlet of the tunnel in the Quibor valley, towards Yacambu. The tunnel, when completed, will be turned over to the Environmental and Natural Resources Ministry of Venezuela.
SIZE / CAPACITY
SERVICES PROVIDED
|
SUPPLIED EQUIPMENT
|